Collection: Friction Stir Welding (FSW) Tools
-
Friction Stir Welding Tool (FSW), FS1, Size 1
Vendor:MEISTERFABRIKRegular price 680 SEKRegular price -
Friction Stir Welding Tool (FSW), FS1, Size 3
Vendor:MEISTERFABRIKRegular price 680 SEKRegular price -
Friction Stir Welding Tool (FSW), FS1, Size 2
Vendor:MEISTERFABRIKRegular price 680 SEKRegular price -
Friction Stir Welding (FSW) Tool Set, FS1, Size 1-3
Vendor:MEISTERFABRIKRegular price 1 900 SEKRegular price
Got questions about FSW? We're here to help you navigate the possibilities.

What is Friction Stir Welding?
Friction Stir Welding (FSW) is a solid-state joining process invented by The Welding Institute (TWI) in 1991. It involves a non-consumable rotating tool with a pin and shoulder that is pressed into the joint line of two workpieces. The tool generates frictional heat, softening the material below its melting point (typically 80–90% of its recrystallization temperature). As the tool moves along the joint, it stirs the softened material together, creating a solid-state weld with fine-grain microstructure and high mechanical integrity.
FSW avoids common fusion welding defects such as porosity and cracking. It is widely used for aluminum alloys, titanium, and other materials in industries such as aerospace, automotive, and marine, with significant advancements driven by NASA for aerospace applications like cryogenic fuel tanks.
How does it handle different materials—aluminum, copper, etc.?
MEISTERFABRIK has conducted exploratory testing of the FS1 Friction Stir Welding (FSW) Tool on various materials, including 110 Cold Rolled Copper Alloy (H02 Temper), 6061 Aluminum (T6511 Temper), and 6082 Aluminum, to assess its compatibility and performance. While the tool demonstrated promising results across these alloys, each material requires tailored parameters to achieve optimal welds, emphasizing the importance of proper setup and control.
Material-Specific Observations
- Copper (110 Cold Rolled Copper Alloy, H02 Temper):
Copper’s high thermal conductivity caused significant heat buildup during testing, requiring active thermal management to avoid overheating the workholding equipment. The FS1 tool successfully joined the material, but users should be aware of the potential for thermal-related challenges and carefully monitor the process. - 6061 Aluminum (T6511 Temper):
This alloy performed well with minimal heat generation under standard parameters. The FS1 tool produced clean, defect-free welds without requiring additional cooling measures, suggesting it is highly compatible with 6061 aluminum when used within recommended settings. - 6082 Aluminum:
Testing with both simple (straight-line) and complex (tricordal) tool paths showed stable welds when using a straightforward approach, with the FS1 Size 2 tool performing efficiently. However, the tricordal path generated excess heat, increasing cycle times without improving weld quality. For 6082 aluminum, simpler welding strategies may yield better outcomes.
Key Considerations
- Each material exhibits unique thermal and mechanical behavior during friction stir welding. Proper calibration and process control are essential to ensure consistent results.
- The FS1 tool performed well within the controlled testing conditions, but real-world applications may involve additional variables, such as differing equipment setups, operator techniques, or material properties.
- For demanding materials like copper, users should prioritize thermal management strategies and ensure their workholding equipment is suitable for high-heat scenarios.
While the FS1 tool is designed to handle a range of materials effectively, MEISTERFABRIK advises users to perform their own testing and parameter optimization to confirm suitability for specific applications. For further guidance, please consult the FS1 tool documentation or contact our support team.
How durable is the tool under consistent use?
The MEISTERFABRIK FS1 friction stir welding (FSW) tool is designed to be a durable and long-lasting solution for a wide range of applications. Under consistent use, the tool can withstand the rigors of the FSW process and maintain its performance over time.
The tool life of friction stir welding tools can be compared to that of an endmill, which is a common cutting tool used in machining operations. While endmills typically have a limited tool life and may need to be replaced frequently, the MEISTERFABRIK FS1 can, under ideal conditions, weld for several kilometers.
Long-Lasting Performance
In fact, the tool life of the MEISTERFABRIK FS1 is often measured in kilometers, rather than hours or cycles. This is due to the unique nature of the FSW process, which uses a rotating tool to generate heat and plasticize the material, rather than relying on a consumable electrode or filler metal.
Factors Affecting Tool Life
While the MEISTERFABRIK FS1 has a long tool life, its performance can still be affected by various factors, including:
- Material type and thickness
- Welding speed and axial force
- Tool rotation speed and direction
- Cooling and heat management
By optimizing these factors and following proper maintenance procedures, the tool life of the MEISTERFABRIK FS1 can be maximized.
What’s the surface finish like on completed welds?
Typical Surface Roughness
With good welding parameters, the surface roughness of the weld typically ranges between:
- 0.8 to 3.2 μm (micrometers)
- 32 to 126 μin (microinches)
Optimal Welding Parameters
To achieve the best possible surface finish, it is essential to optimize the welding parameters, including:
- Welding speed
- Tool rotation speed
- Tool pressure
- Cooling and heat management
Post-Weld Processing
While the surface finish of welds produced by the MEISTERFABRIK FS1 is typically smooth, some post-weld processing may be necessary to remove flash formation. This may include:
- Light filing, machining, or grinding to remove any minor flash or imperfections
- Polishing or buffing to achieve a high-gloss finish
Will it integrate easily into my current equipment, or do I need to modify my setup?
The MEISTERFABRIK FS1 friction stir welding (FSW) tool is designed to be a versatile and adaptable solution for a wide range of applications. In most cases, the FS1 can be easily integrated into your current equipment setup with minimal modifications.
Compatibility with Manual and Power Feed Milling Machines
The MEISTERFABRIK FS1 has been thoroughly tested and is compatible with both manual and power feed. This means that you can easily apply the same metal cutting knowlegde to aluminium welding.
Tool Holder Compatibility
The MEISTERFABRIK FS1 can be used in a variety of tool holders, including:
- R8
- CT40
- SK40
- BT40
These tool holders can be equipped with different styles of collets or holders, such as:
- ER
- 1/2 inch endmill holders
- Shrinkfit
Minimal Equipment Requirements
To ensure optimal performance, the MEISTERFABRIK FS1 requires a minimum of:
- 2 HP (horsepower) or 1.5 kW (kilowatts) of power
- 2000 RPM (revolutions per minute) of spindle speed
- 20 Nm (newton-meters) or 14.75 lbf-ft (pound-feet) of torque
- 1000 N (newtons) or 225 lbf (pounds) of axial load
Additional Thermal Considerations
In heavy welding applications, additional heat sinking or cooling equipment may be necessary to ensure optimal performance and prevent overheating of the work and tool holding equipment. This may include the use of cooling systems, heat exchangers, or other thermal management solutions, or backing with high thermal conductivity (aluminum).
If your milling machine meets these requirements, you can readily integrate friction stir welding process in your shop.
How much effort goes into preparing the material and the tool for use?
The simplicity of the preparation process makes FSW an attractive option for a wide range of applications, from aerospace and automotive to construction and manufacturing. As the process requires minimal preparation to produce quality aluminum welds. When using the MEISTERFABRIK FS1 FSW tool, the preparation process is straightforward and efficient.
Basic Preparation Requirements
To ensure successful FSW with the MEISTERFABRIK FS1, the following basic preparation steps are recommended:
- Secure Fixation: Properly and securely fix the base material to prevent movement during the welding process, just as any typical machined part.
- Equipment Settings: Set the MEISTERFABRIK FS1 to the appropriate feed and speeds for the specific material being welded. This ensures optimal weld quality and minimizes the risk of defects.
- Surface Cleaning: While not strictly required, light cleaning of the workpiece surface is recommended to minimize contamitation from dirt and oil.
- Proper Heat Sinking or Cooling: Ensure that the workpiece is properly heat sunk or cooled, where necessary, to avoid thermal damage to the workholding tools and other equipment.
By following these basic preparation steps, you can achieve high-quality welds with the MEISTERFABRIK FS1 FSW tool.
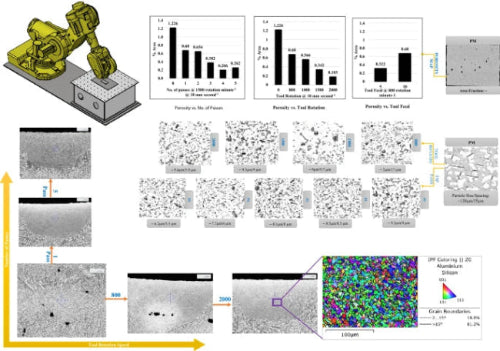
Stirring-Edge Research
"This endeavour is to augment mechanical attributes via friction stir processing in hypereutectic al–si castings by means of microstructural modifications and defect reduction. The study proceeds with mainly two approaches namely, alteration in tool revolution and the number of FSP passes. Specimens were evaluated investigating volume fraction of porosities, microstructural characterizations and microhardness."
Whats going on here?
If you manage to look past the mayhem that is our workbench (don't worry, it's just part of the creative process), you'll spot something truly magnificent: a Haas Mini Mill humming away at 2100 RPM, with an FS1 Size 2 Friction Stir Welding Tool mounted in the spindle via a CT40 ER32 tool holder. It’s like a perfectly choreographed fight scene between metal and machine, with axial and radial feedrates cruising at about 180 millimeters per minute (or 7 inches per minute, for those who understand fractions).
What's it up to, you ask? It's joining 6082 Aluminum alloy plates with the finesse of a well-timed plunge and push, using another 6082 bar for backing. The result? A weld that’s not just strong—it’s the kind of bond that makes you feel like a mad scientist, ready to slingshot your next satellite into orbit.
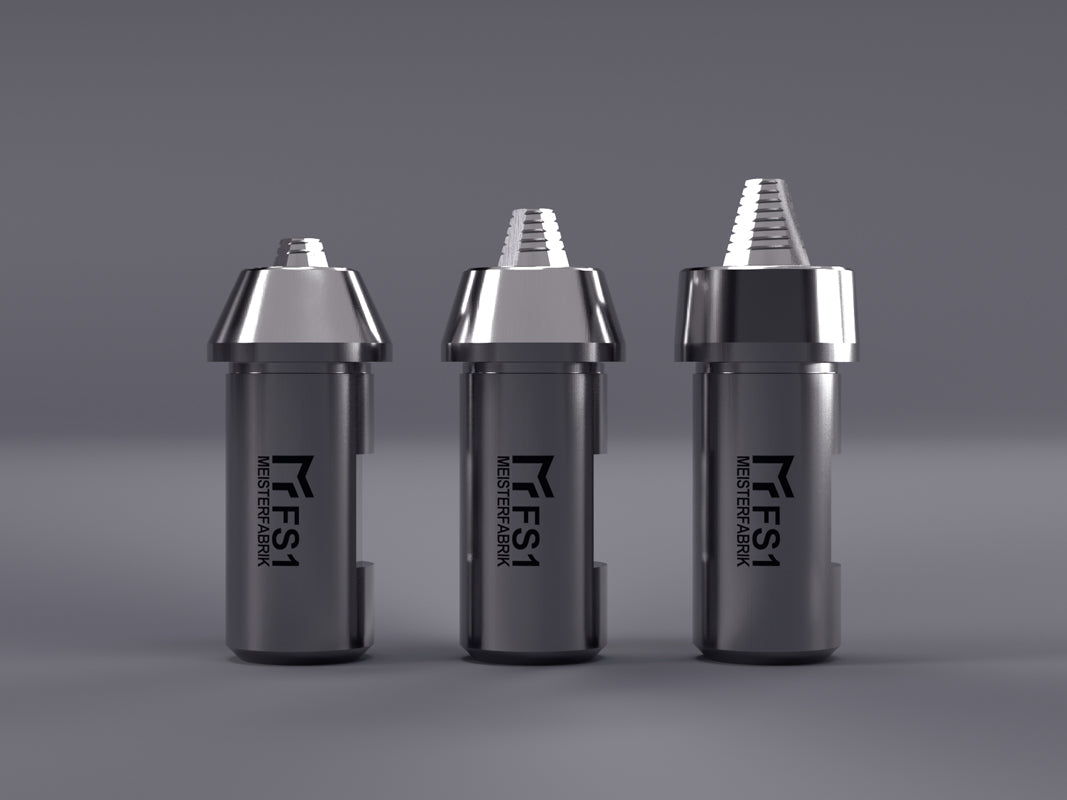